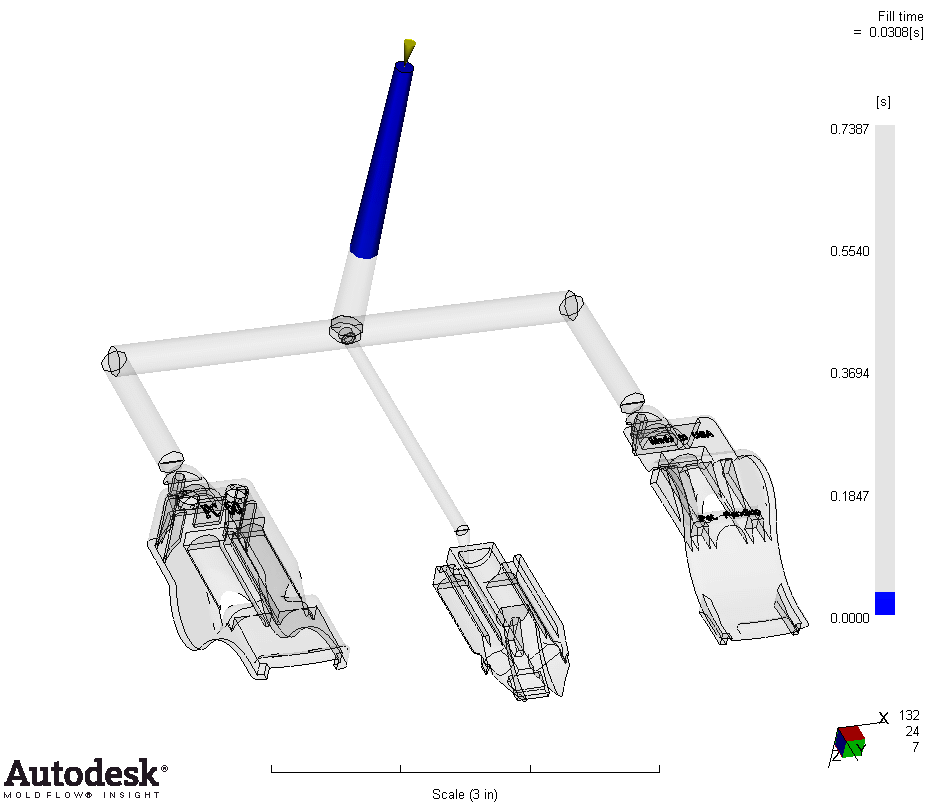
Filling Simulation
Determine optimum number of gates, pressure to fill, weld line and air trap locations, balance runners and more!
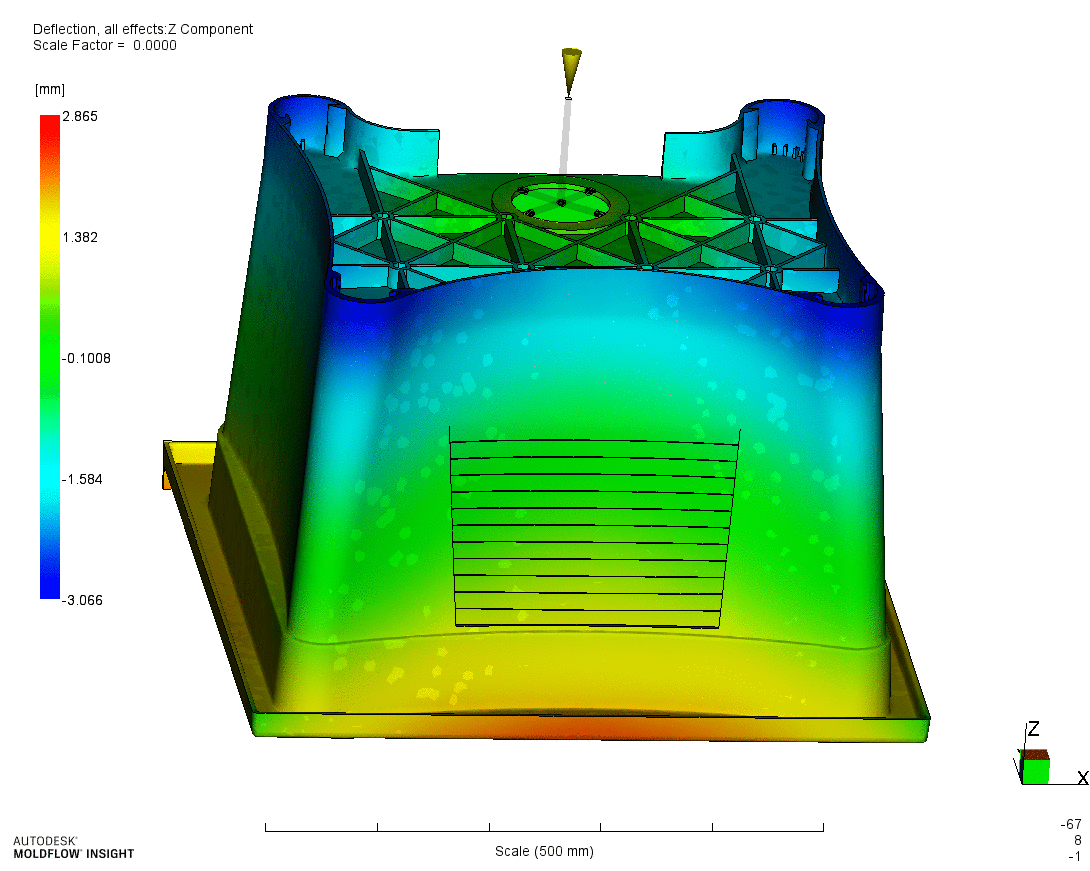
Warp Simulation
Warp simulation uses data calculated by the fill, pack and cooling analysis to provide warp predictions. It also contains a diagnostic tool to provide information as to what is the cause of the warp to guide corrective action.

Structural Analysis (FEA)
FEA considers a force applied to a part and the resultant stresses and deflections. Examine different materials, wall thicknesses, and geometry changes such as adding ribs or gussets.

Design Assistance
We can create conceptual designs, provide design reviews and assist with design changes using Solidworks CAD software.

Material Selection
Our plastic materials knowledge will guide you to select the right family of materials for your application. Using an additional layer of analysis tools, such as flow analysis and FEA, we can make sure you are choosing the correct grade of material for optimum part performance.

Packing Simulation
The main objective of a packing analysis is to achieve uniform shrinkage across the part, which can reduce warp and dimensional instability. Also identify where possible sinks and voids can occur and more!

Cooling Simulation
A Cooling analysis can identify any hot spots in the tool and provide guidance on where to move or add cooling lines. This will reduce cycle time and provide a more dimensionally stable part. This analysis can also provide estimated cooling times for your part as well as pressures, flow rates and temperatures for the cooling lines.
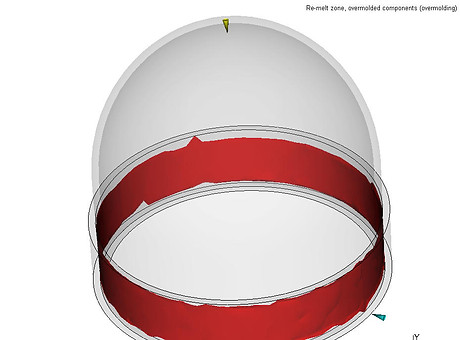
Overmolding Simulation
Either an insert type overmold analysis (made from any material), or a two shot overmold analysis can be performed to see how two different types of plastics interact when molding.

Autodesk Moldflow Training
Training in Autodesk Moldflow "Fundamentals", "Advanced Flow" and "Advanced Cool and Warp".